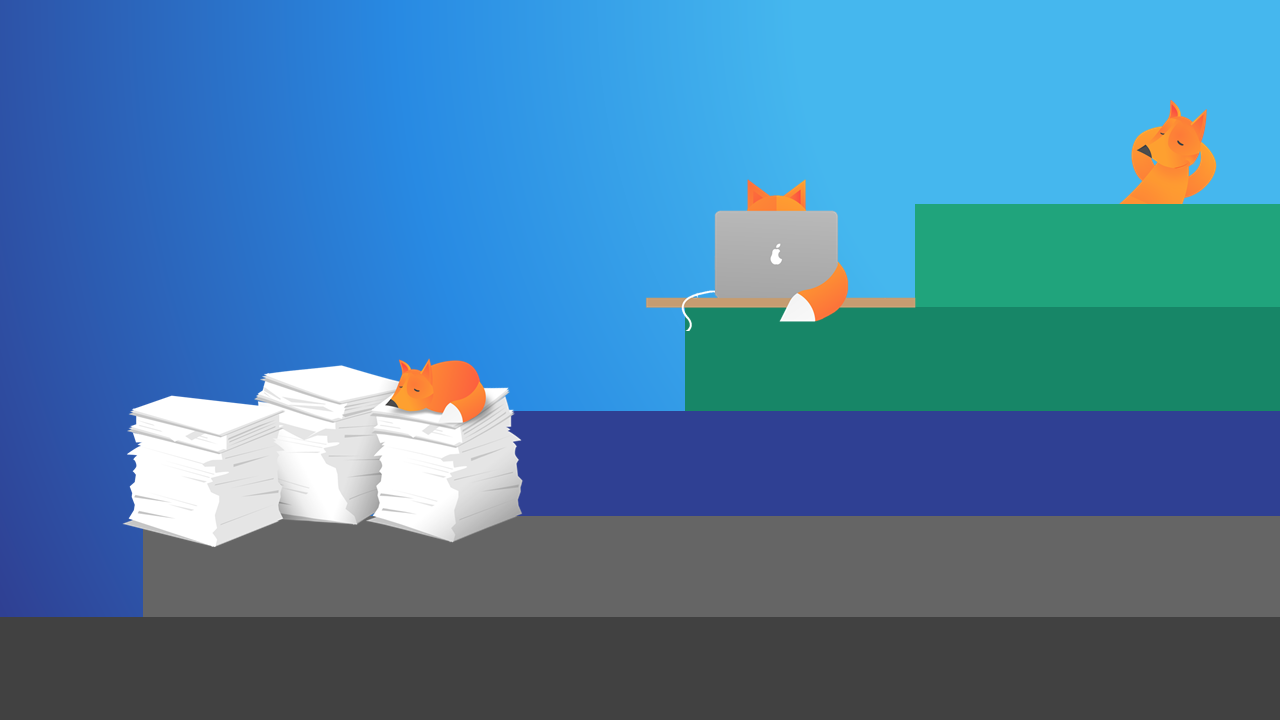
Years of working closely with laboratories have taught us that the mindset in different organizations towards validations and verifications – and quality in general – varies a lot. The benefits a customer gets from using Validation Manager depend surprisingly much about this mindset.
To reach full potential in quality, you need to focus on improvement and moving forward. And to be able to form realistic expectations for that process, it’s important to first understand where you stand. That way you can set your goals for incremental improvements wisely.
From our experience we’ve outlined five quality steps that represent these different mindsets you can find in a laboratory. While a laboratory is very rarely in the lower steps in all areas, some things may have been overlooked, or all quality practices may not have reached all departments. Some customers may also find themselves in between two steps. Which ones of them describe your laboratory best?
Quality step 0 – Starting out
There are some small laboratories that seem to rely on their luck. They run commercial tests and trust that since the manufacturer has stated that a test or an instrument works, it must be just fine. They are not accreditated, and may not be forced to follow any standards, so they get to run their business pretty much as they find convenient.
These labs run controls only because that’s what the instructions tell you to do. Control results are not evaluated as a sign of possible problems with the test or the instrument. Instead, failed controls are rerun until acceptable results appear. And if the evaluation of the acceptability of control results is purely manual, it may be that no-one ever really evaluates them.
With these kind of laboratories, what is needed is some kind of a wake-up. They need to realize that they have to do something to start climbing up the quality steps. Unfortunately this may be difficult to achieve without a real incident of compromised patient safety. But if someone within the organization is willing to work hard to push for a change, anything is possible.
Quality step 1 – Passing accreditations
Whether a laboratory is accredited or not, it may perform validations, verifications and external quality assessment (EQA) only to fill out the required forms. Someone has maybe decades ago created a process that is still followed because that way things have always worked out just fine. Changing anything feels scary, as that might provoke new kinds of questions. It feels safer to do things just the way they have always been done. Yet practices may vary between departments and personnel.
Instructions for validations and verifications are based on outdated guidelines and unstandardized practices. Measured results are typed manually to Excel sheets, adding typos as a source of error to the results. There are no performance goals, or the goals are not clinically relevant. Result analysis is subjective, and the relevance and reliability of results is questionable. There is no overview of parallel instrument performance, especially between labs. Measurement uncertainty is not evaluated, or it is done as a subjective estimate of error sources to fill accreditation needs.
EQA is done with manual Excels. The goal is just to pass the rounds, results are not used to improve quality and may even be looked at only when preparing for quality audits.
There is no overall visibility to quality and not much focus on improving quality.
What these laboratories need is a mindset change. They need to learn to see validations, verifications and EQA as tools for assuring and improving quality. And they need to see that quality matters, and that they have the power to affect it. With this realization, they will be able to get to the next level.
Quality step 2 – Focus on quality
Many laboratories have a very good mindset towards quality. In validations and verifications, latest guidelines are followed, and performance goals are set up. Results are analyzed objectively, based on relevant statistics, and there are individual quality improvement initiatives. Results of EQA rounds are analyzed to improve quality.
There may still be huge differences between departments on how well verifications are done. This is because the amount of manual work and complexity of statistics make verifications dependant on the expertise of the individual people performing the verifications.
A common problem is a lack of sufficient tools. There may be many tools to help with individual tasks, but mostly things are managed and analyzed in Excel sheets. Data and results are analyzed individually, stored in files, folders and network drives. Everyone may use different kinds of Excels for their verifications, making it difficult for others to understand them. Additional Excels are needed to manage where to find data and calculations. Finding things takes time, and there is no overall visibility or transparency. If there is something puzzling on a report, there is usually no way to find out what has happened.
Due to a lack of tools, a typical reason for not passing an EQA round is that sample results have been mistakenly mixed or a number has been typed incorrectly.
For a laboratory like this, Validation Manager and EQA Manager as software solutions help them get their work on the next level.
Quality step 3 – Standardize, digitalize, automate
More and more laboratories are finding the benefits of using automated tools in validations and verifications. Their processes and practices are standardized through all departments and laboratory locations, even though that has required some readjustment and settlement. This way everyone understands each other’s work.
They do periodic instrument comparisons, since with proper tools that doesn’t feel like an unreasonable effort. As most things are automatized, there is time for improvement and concentrating on what’s relevant. Verification analysis focuses on important issues. Use of Excels in data management is minimized to prevent mistakes in manual work.
Validation and verification reporting is digitalized, as well as EQA process, giving overall visibility to quality. Results are reliable and comparable.
This may already seem like a dream come true, but even these laboratories have room for adding automation and making data management easier for them. The mindset change they need is to figure out that automation and modern solutions can give them much more than just a set of tools to help in old practices. They could see and do things that weren’t possible before. When they realize this, they are ready to get to the next level.
Quality step 4 – Lab 4.0
What laboratory quality management can be, is a system where all data is automatically available in one place. Through LIS or middleware integration data is periodically uploaded to Validation Manager. That way verifications and continuous improvement become an effortless and natural part of laboratories everyday work.
Control performance is monitored centrally. EQA is done proactively, using results to improve quality. There are new insights into quality, for example in controlling parallel instrument performance in remote laboratory locations.
As there is real time visibility to laboratory performance, there is confidence in results and quality.
Where are you standing – and where would you like to be?
Regardless of where you find your laboratory, there is room for improvement. We at Finbiosoft are happy to help you up on these steps. What we provide are tools, training and consultation to get you to step 3 and from there to step 4.
If you are already on step 2, getting on-board is quite easy as it’s mostly about learning to use a new tool.
We are also trying our best to wake up laboratories on step 0, and introduce seeds for a mindset change for laboratories on step 1. But these things are more about organization culture, management and leadership. An outsider cannot create a change, unless the organization is willing to follow. The further you are from step 2, the slower and more difficult the process of improvement may feel. Sometimes it can even feel a little painful, as you are faced with the cold truth about the justification of your old practices.
But knowing what the future could hold, it’s worth it.
Would you be the champ to promote a change for something better? Take the next step and reserve a consultation with us!
Accomplish more with less effort
See how Finbiosoft software services can transform the way your laboratory works.